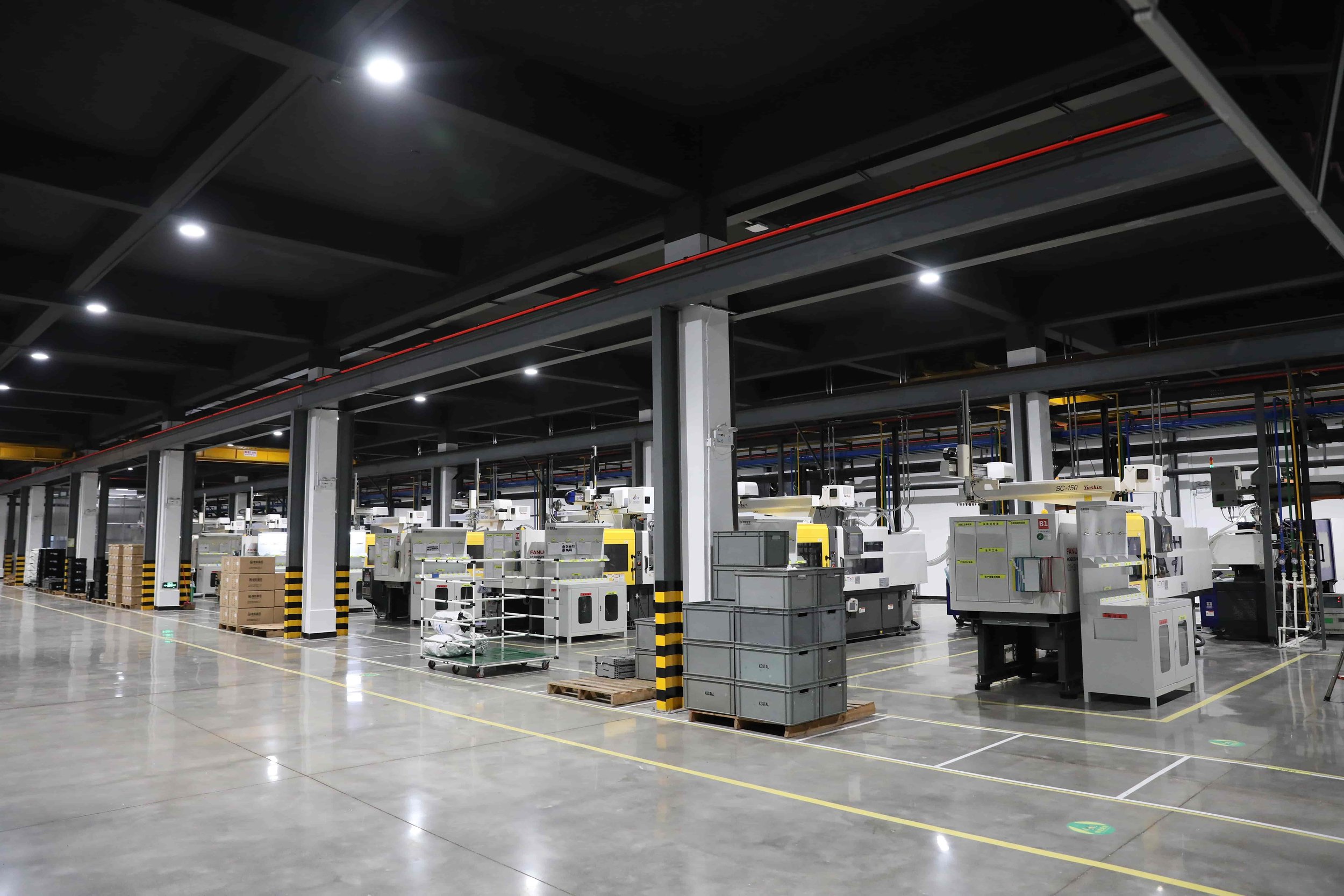
Family-owned since 1985
We provide you one-stop manufacturing services including 3D printing, tooling, moulding, die casting and secondary processes.
TS6949:2016 & ISO 9001:2008 Certified
Conformal Cooling Channels
Conformal Cooling Channels in Mold Making: Enhancing Efficiency and Quality
Introduction
In modern injection molding, improving efficiency and part quality while reducing cycle time is crucial for manufacturers. One of the most innovative advancements in mold design is the integration of conformal cooling channels. Unlike conventional straight-line cooling channels, conformal cooling follows the shape of the mold cavity, offering uniform heat dissipation and superior temperature control.
This article explores the concept, benefits, manufacturing techniques, and applications of conformal cooling channels in mold making.
What is Conformal Cooling?
Conformal cooling refers to the strategic design of cooling channels that follow the contours of the mold cavity, ensuring even heat distribution. Traditional cooling channels, typically drilled in straight lines, often leave hot spots, leading to inconsistent cooling and defects such as warping or shrinkage.
Conformal cooling addresses these issues by optimizing heat transfer, leading to improved cycle times and part quality.
Benefits of Conformal Cooling Channels
1. Reduced Cooling Time & Cycle Time
Cooling accounts for 50-70% of the injection molding cycle. Conformal cooling improves heat transfer efficiency, reducing cooling time by up to 30-50%, which directly translates to shorter cycle times and higher production rates.
2. Improved Part Quality
Uneven cooling can cause warping, sink marks, and internal stresses. With conformal cooling, uniform temperature control minimizes these defects, resulting in parts with higher dimensional accuracy and better surface finishes.
3. Energy Efficiency & Cost Reduction
Better cooling reduces the need for extended holding pressure and cooling durations, saving energy and lowering operational costs. It also minimizes scrap rates and rework costs due to fewer defective parts.
4. Enhanced Mold Longevity
Conformal cooling ensures even temperature distribution, reducing thermal stress on the mold, which helps prevent premature wear and extends the mold’s lifespan.
5. Design Flexibility for Complex Parts
Since conformal cooling can be customized to any shape, it is particularly beneficial for complex and intricate geometries, where traditional cooling methods are inefficient.
Manufacturing Techniques for Conformal Cooling Channels
To create conformal cooling channels, traditional drilling techniques are inadequate. Instead, advanced manufacturing technologies are employed:
1. Additive Manufacturing (3D Printing)
Selective Laser Sintering (SLS) and Direct Metal Laser Sintering (DMLS) allow the creation of intricate cooling channels within molds.
Metal 3D printing enables complex lattice structures for optimized heat exchange.
Common materials: Stainless steel, maraging steel, and aluminum alloys.
2. EDM (Electrical Discharge Machining)
Used in combination with traditional CNC machining, EDM can create curved cooling channels by removing material with electrical discharges.
Effective for hard metals but has higher costs and longer processing times than additive manufacturing.
3. Laser Drilling & Milling
Laser drilling can create intricate, small-diameter cooling channels in hard tool steels.
CNC milling can assist in semi-conformal cooling by machining curved grooves before sealing them with inserts.
Applications of Conformal Cooling Channels
Conformal cooling is widely applied across industries where precision, efficiency, and cost-effectiveness are essential:
1. Automotive Industry
Used in plastic components like bumpers, dashboards, and lighting systems.
Reduces cycle times for high-volume production, improving manufacturing efficiency.
2. Medical Industry
Essential for high-precision medical device components such as syringes, catheters, and prosthetics.
Enhances accuracy and biocompatibility by minimizing material stress.
3. Consumer Electronics
Helps in producing complex phone casings, laptop covers, and connectors with tight tolerances.
Ensures uniform cooling for improved product quality.
4. Aerospace & Defense
Used in lightweight, high-strength polymer parts for aircraft interiors and defense applications.
Maintains structural integrity by reducing residual stress in injection-molded components.
Challenges and Considerations
1. High Initial Cost
Additive manufacturing and advanced machining processes require higher upfront investments compared to traditional mold-making methods.
2. Design Complexity
Requires specialized software such as Moldflow, SOLIDWORKS, or Autodesk Fusion 360 for simulation and optimization.
3. Material Compatibility
Not all mold materials are compatible with additive manufacturing techniques, limiting options for certain applications.
4. Maintenance and Cleaning
Complex cooling channels may clog over time due to coolant impurities, necessitating regular cleaning and maintenance.
Conclusion
Conformal cooling channels represent a significant advancement in mold making, offering faster cycle times, improved part quality, and cost savings. With the rise of additive manufacturing and advanced machining, more industries are adopting this technology to enhance efficiency and competitiveness.
While initial investment and design complexity remain challenges, the long-term benefits make conformal cooling an indispensable solution for modern injection molding.
Future Outlook
With advancements in AI-driven mold design, computational fluid dynamics (CFD) simulations, and hybrid manufacturing techniques, conformal cooling is set to become even more efficient, accessible, and cost-effective in the coming years.