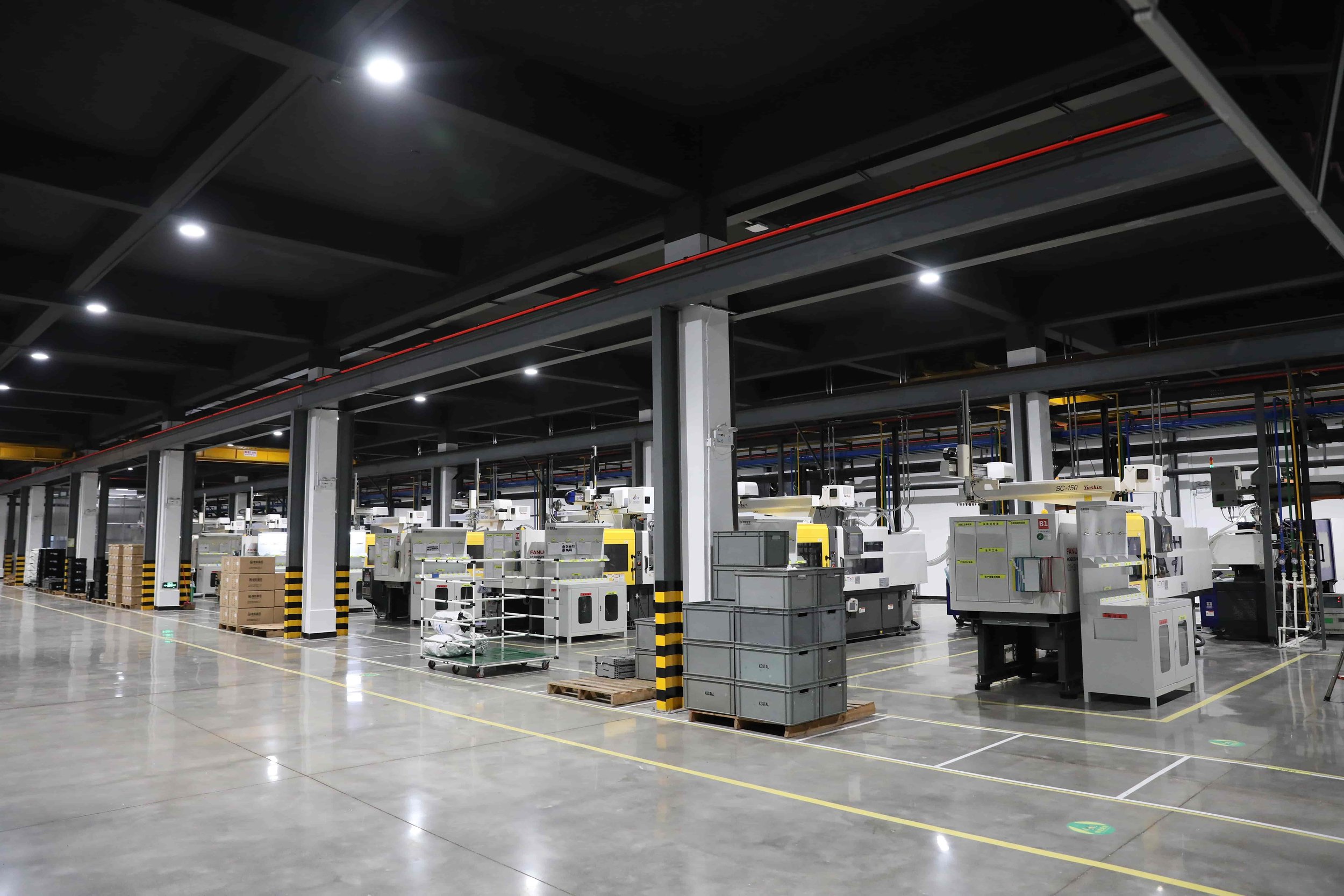
Family-owned since 1985
We provide you one-stop manufacturing services including 3D printing, tooling, moulding, die casting and secondary processes.
TS6949:2016 & ISO 9001:2008 Certified
Stack Molds and Moulding
Stack Injection Molds and Moulding:
Boosting Efficiency in High-Volume Production
In the fast-paced world of plastic manufacturing, efficiency, speed, and scalability
are crucial. One powerful technique that delivers on all three fronts is stack injection
molding. While traditional injection molding has long been the industry standard,
stack molds offer a smart evolution—especially when it comes to high-volume production with tight timelines.
What is Stack Injection Molding?
Stack injection molding refers to a specialized injection molding technique where multiple mold parting lines (or mold faces) are stacked within a single mold base. Think of it as having two or more molds working in parallel within one machine cycle.
Instead of placing all cavities on a single plane, the stack mold divides them across two or more levels (or "stacks"), arranged around a central rotating or sliding axis. This setup allows manufacturers to double or triple output without increasing the footprint or tonnage of the injection molding machine.
How It Works
At its core, the process of stack molding is similar to conventional injection molding:
Plastic resin is heated and injected into the mold.
The material fills the cavities and is cooled to form solid parts.
The mold opens, and the parts are ejected.
What makes stack molds different is the way the cavities are arranged. In a 2-level stack mold, for example:
Half the cavities are located on one side of the center plate.
The other half are mirrored on the opposite side.
A rotating center block or side sliders help distribute the melted plastic equally across both levels.
This design makes it possible to mold twice the number of parts per cycle, improving productivity dramatically.
Key Benefits of Stack Molds
1. Increased Productivity
The most obvious benefit is higher output per machine cycle. Without increasing the cycle time, you can produce twice (or more) the number of parts compared to a single-face mold.
2. Reduced Machine Footprint
Instead of installing multiple machines or larger presses, you can use one stack mold in a standard-sized machine, conserving floor space and infrastructure costs.
3. Lower Cost per Part
Although stack molds have a higher upfront cost, the increase in productivity reduces the cost per unit, especially for long-run production.
4. Energy Efficiency
With more parts produced per cycle, the energy cost per part goes down. This contributes to sustainable manufacturing goals.
5. Optimized Cycle Time
The cooling time remains the same as in a standard mold, meaning the overall cycle time doesn't increase despite the higher output.
Design Considerations
While stack molds offer numerous advantages, they do come with design challenges:
Precision is critical: Each stack must be perfectly aligned to ensure proper flow and uniform pressure distribution.
Cooling and venting need to be carefully planned, as the internal stack levels can be harder to cool uniformly.
Ejection mechanisms must be duplicated or synchronized for each stack.
Mold balancing: Flow channels (runners) must be optimized to ensure equal fill across all cavities.
Because of this complexity, stack molds are typically best suited for high-volume, consistent parts such as packaging, medical devices, caps and closures, and thin-walled containers.
Common Applications
Stack molding is widely used in industries where speed, precision, and cost-efficiency are critical:
Food and beverage packaging
Medical disposables (syringes, pipettes)
Cosmetic containers
Automotive connectors and components
Consumer electronics
Stack injection molding is a powerful solution for manufacturers looking to scale up production without scaling up equipment costs or floor space. Though it demands a higher level of engineering, the long-term return on investment can be significant.
For businesses targeting leaner operations, higher throughput, and lower part costs, stack molding is more than just a technical upgrade—it’s a competitive advantage.